Hydrophobic silica is a kind of silica which is modified by liquid phase in-situ surface modification technique using dimethylsilane as the main modifier. The primary particle size is less than 25um, the particle size of the polymer is about 5 microns, the content of SiO2 is not less than 99.8%, and it is a multi-functional additive.
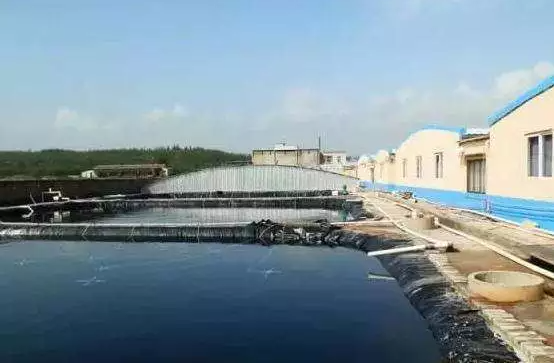
As an important additive in industry, the amount of defoamer is small but indispensable, and it is widely used in various fields such as textile, paper making, petroleum, food and medicine. The defoamer is specific and specific, because the foaming mechanism and process conditions of each foaming system are different, and different foaming systems require different defoamer. It can be roughly divided into non-silicon system and silicon system defoamer. Non-silicon systems such as higher alcohols, acids, hydrocarbons, polyethers, esters, phosphate esters, etc., their quantities are large and their applicability is small; Silicon defoamer is the main component of silicone oil/silica black silicone oil paste and modified silicone oil, which is the most widely used and most efficient defoamer at present.
Silicon defoamer has several outstanding features compared with other types of defoamer:
1. Dispersion effect: An important indicator to measure the quality of defoamer is its dispersion effect. Only substances with small solubility and large dispersion can become the active ingredients of defoamer. As the main component of defoamer, dimethylsilicone oil has small solubility and small dispersion. It must be improved by means of white carbon black, emulsifier and other dispersion additives. Due to the existence of SiO2 particles, silicone oil can be quickly spread in the foaming liquid, improving the dispersion efficiency of silicone oil, thereby improving the antifoaming effect. Therefore, hydrophobic silica is used as a very important dispersant in defoamer.
2. Adsorption: An important role of SiO2 in defoamer is adsorption. Due to the small particle size, large specific surface area, high surface energy and three-dimensional network structure, SiO2 can form a huge adsorption force of bubbles, which together with silicone oil forms a force to attack bubbles, that is, SiO2 adsorbs and impacts bubbles to cause weak points, and bubbles rupture under the action of low surface tension of silicone oil, resulting in bubble bursting. Therefore, SiO2 is equivalent to the "tip of the needle" in the defoamer, and the amount is small but the effect is huge. It and silicone oil, as the active ingredients of high efficiency defoamer, have compound, high efficiency and synergistic defoamer effect.
3. Thickening and anti-settling effect: The important index of emulsion type silicone oil defoamer is the defoamer effect and storage stability, especially the silicon-containing cream emulsion. There are many reasons affecting the stability of the emulsion, such as the particle size of the emulsion, the viscosity of the emulsion and so on. Emulsion particle size is the most important control index of emulsion defoamer, and the particle size is generally required to be less than 10um. The size of the emulsion depends on the choice of emulsifier, the emulsification process and the size of the particles. The minimum particle size of hydrophobic silica can reach about 5um, and the silicone oil emulsion particles containing such SiO2 form a basic defoaming unit with very small particles and a large number of particles in the foaming solution, so that the defoaming agent can achieve the best defoaming effect. At the same time, due to the small particle size, large specific surface area, and stable hydrogen bond three-dimensional network structure, SiO2 particles can be evenly and stably distributed in the entire system, so that the storage of the system is stable.