制浆过程中,为了获得白色的纸浆,木片会经过蒸煮、洗涤和漂白等流程(图1),不过在这一系列纤维处理过程中,消耗了大量水,也会产生大量泡沫,因此选择合适的消泡剂十分关键
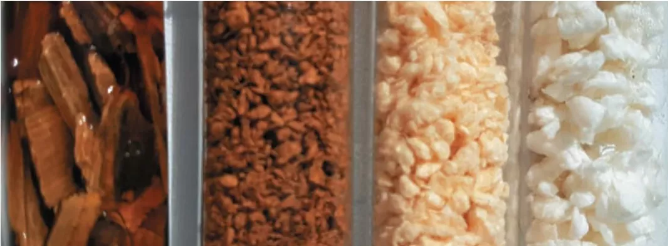
Figure 1: Wood chips, pulp after cooking, pulp after washing, and bleaching
Over the years, the paper industry has made many efforts to reduce energy, water and chemical consumption in order to achieve sustainable development, and the use of silicone defoamer is one of them. The use efficiency of silicone defoamer is high, which can greatly improve the sustainable development index of pulp and paper enterprises.
Silicone is a kind of polymer material, in which polysiloxane is mainly composed of silicon-oxygen bond as the skeleton, and the structure is shown in Figure 2. It represents the infinite possibilities of polymers, and changes in the length of the chain, the three-dimensional structure, and the type of organic group attached to the silicon atom can all affect the properties of silicone.
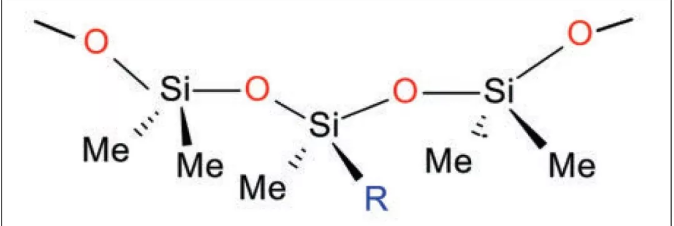
Figure 2 Polysiloxanes with organic groups
The silicone oil used in defoamer is a polymer with high hydrophobicity and extremely low surface tension. Once polydimethylsiloxane (PDMS) is combined with hydrophobic particles (such as precipitated or vaporized silica), a more effective defoamer is formed, as shown in Figure 3.
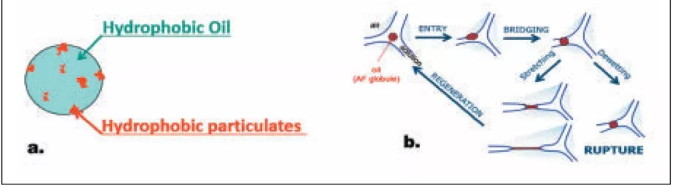
FIG. 3 Action flow of defoamer
Silicone defoamer began to be used in the pulping process in the 1980s, solving the problem of low efficiency of traditional organic defoamer. Silicone defoamer can adapt to the pH environment and high temperature conditions, and replaced the original defoamer almost overnight. The simple structure and convenient use of organosilicon have also laid the foundation for the development of high-end defoamer in most paper mills.
Although silicone defoamer has many innovative advantages, it also inevitably causes some problems, such as the risk of precipitation, residual contamination, emulsification, scaling and so on.
Precipitation risk
Because silicone is hydrophobic, it has a high affinity with any hydrophobic surface, the high pH value and high temperature of the liquid can promote the condensation of the residual activity of the silicone compound, and promote the formation of the gel, forming a precipitate.
The analysis shows that the formation of precipitation is caused by many factors, including the chemical composition of silicone defoamer. Precipitation is a concern for all pulp mills because the production of precipitation during the pulping process increases the cleaning cost of the pulping line.
The risk of precipitation formation depends on the composition of the defoamer, the quality of the reagent, the dose and the method of use. Therefore, pulp and paper enterprises can reduce the precipitation risk from the following aspects:
First, appropriately reduce the dose of defoamer. The use of effective defoamer is very critical, but excessive use will produce precipitation, so the dosage of defoamer should be controlled during the pulping process, and should not be used too much.
Second, select a defoamer with less residual substance, and ensure that the remaining substance of this defoamer cannot continue to react chemically with the alkaline environment, thus significantly reducing the precipitation amount.
Third, using the correct formula, the defoamer compound is emulsified so that it can be dispersed in the foamed black liquor.
Drainage problem
In addition to reducing precipitation, the ability to drain water is also critical for defoamer. Strong drainage means that the pulp mill can use less water to clean the pulping black liquor and quickly discharge the water, which helps to improve the drying efficiency of the slurry in the later period. This is not only conducive to foam control, but also significantly improves the effectiveness of washing slurry and production sustainability, which is an important reason to choose silicone defoamer.
Therefore, although silicone defoamer has the risk of precipitation, but through effective use, can reduce pulping energy, water and chemical consumption, for the paper industry, it is still a sustainable and efficient defoamer technology.