Study on high temperature resistant silicone / epoxy resin powder coating for automobile exhaust pipe
1.3.4 preparation of coating
The preparation of coating includes degreasing, derusting and electrostatic spraying.
The cold-rolled sheet was immersed in hot acid and hot alkali to remove rust and protective oil. The immersion time was 7-10min. After treatment, dry naturally. By electrostatic spraying, the powder was sprayed on the cold-rolled plate, and solidified at 230 ℃ for 30 minutes, then the high-temperature resistant powder coating was obtained. The film thickness was about 60-80 μ M.
1.4 analysis and test
1.4.1 high temperature test
Put the above-mentioned cured tinplate with high temperature resistant powder coating in muffle furnace, bake at 600 ℃ for 1h, and take it out for performance and coating color difference analysis after baking.
1.4.2 other performance tests
The color difference analysis of the coating was carried out with the color difference instrument, and all the test procedures were carried out at room temperature (23 ± 2 ℃); the coating performance was tested with qcj film impact resistance device: the coating performance was tested according to Hg / T 2006-2006, and the coating adhesion was tested with the grid method.
2 results and discussion
2.1 selection of pigments and fillers
Pigments and fillers are the most important part besides resins, which are directly related to the decoration and heat resistance of coatings. According to the literature, silicon material, barium sulfate, talcum powder, mica powder, glass powder and ferromanganese black are the most commonly used pigments and fillers in high temperature resistant coatings. In this paper, the above pigments and fillers on the market are tested for high temperature resistance, mainly for volatile matter and color difference. The test method of color difference is to weigh the fillers before and after baking according to the formula in Table 2, prepare powder coating according to 1.3.3, then prepare coating according to 1.3.4, and then test color difference according to 1.4. The test results of volatile matter and color difference are shown in Table 3.
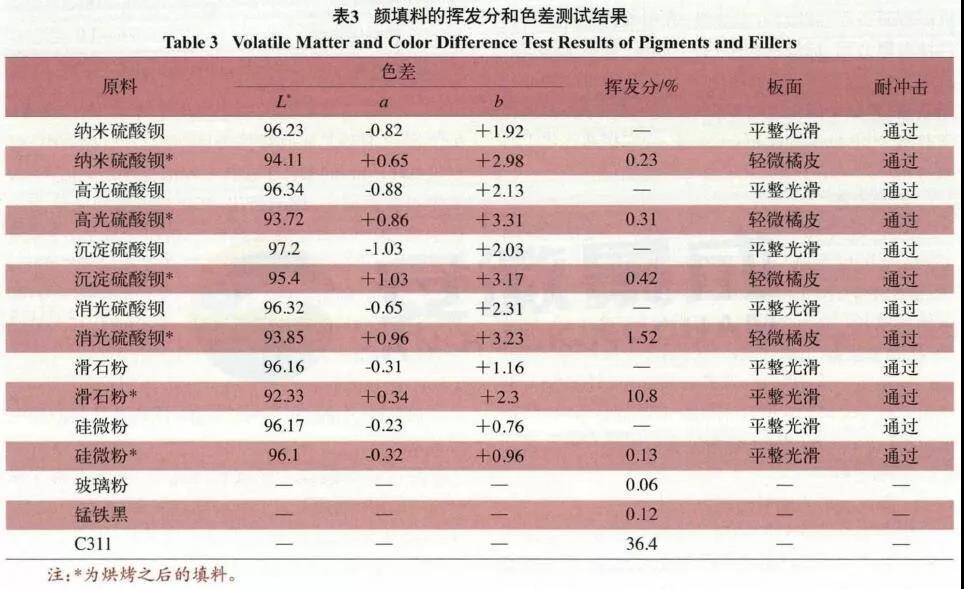
It can be seen from table 3 that the lowest volatile content of glass powder is 0.06%: the second is ferromanganese black, which is 0.12%; the second is silicon micro powder, which is 0.13%; the second is extinction barium, which is 1.52%; the highest volatile content of C311, which is 36.4%, can not be used for high temperature powder coating; the second is talcum powder, which is 10.8%, but its linear expansion coefficient is large, and its volume expansion is large The coefficient is small, which can change the crack resistance at high temperature.
It can be seen from table 3 that the lowest color difference is silica micropowder, followed by precipitated barium sulfate, and then nano barium sulfate. Even though the color difference between precipitated barium sulfate and nano barium sulfate is good, the color difference is still greater than 2, which can be seen by naked eyes. Therefore, silica micropowder is selected as the main filler in this experiment. The high temperature resistant powder coating in the market is mainly black, so the next black pigment is ferromanganese black.
Wen / LV Ying 1, bu Qingpeng 2, Wang Xiaoqiang 2, pan Jianliang 2